The P-NET Fieldbus
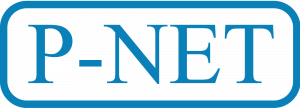
P-NET is an international fieldbus standard (IEC 61158 type 4)
A fieldbus is an electrical means of sending digital messages along a piece of wire between two or more fieldbus nodes (pieces of electronic equipment connected to the fieldbus). A fieldbus standard specifies how messages are sent and received (called the protocol), how collisions of data are avoided, how many nodes can be connected at the same time, timings, type of wire etc.
Apart from designers of new equipment, users do not normally require such detailed information. However, there are certain aspects of the P-NET fieldbus that are unique in terms of fieldbus technology, and which need to be understood by system designers, and installation and maintenance engineers alike, to ensure that the best result can be obtained from a system design.
P-NET uses a principle called Master/Slave. A Master device is one which has the ability to start communication between it and another device connected to the fieldbus. A slave device is a device that can only respond to a message sent to it by a master.
P-NET is also what is known as a Multi-master fieldbus type. This means that up to 32 master devices can be connected to a single P-NET cable, and messages between any of these masters and a slave is controlled so that only one of them transmits at a time (token passing)
P-NET allows up to 125 devices (masters and slaves) to be connected to a single P-NET cable at any one time. It also allows devices to be removed or installed without interfering with messages between other devices.
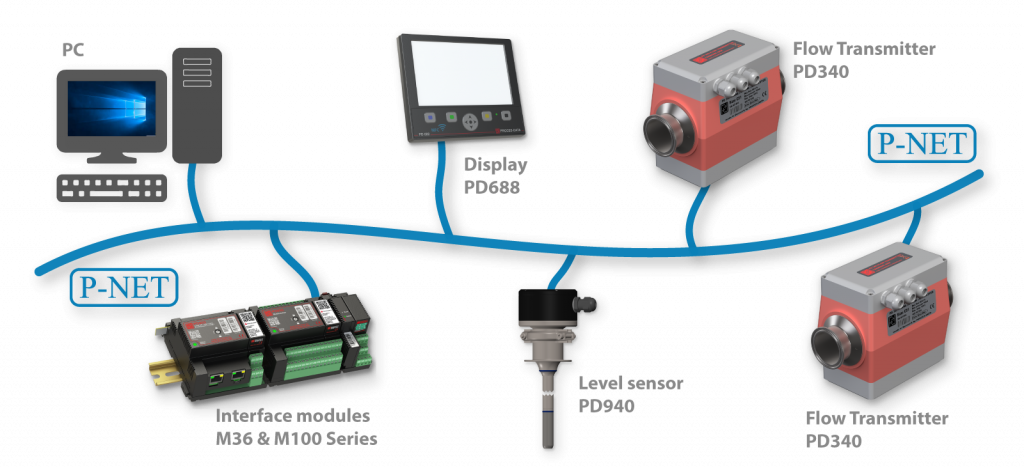
Each device is configured during installation to have a unique number called the node address. This number is used during the transmission of messages to identify the slave address and also the master device’s address that sent it. When a slave responds to a master, it knows which master to send it back to. Normally masters are set with numbers between 1 and 32, and slaves use node addresses between 33 and 125.
A Master device is sometimes called a “Controller” or “DPI” (Distributed Process Intelligence). This is because these are normally programmable devices (in Process Pascal), and it is the program that defines where it requires information to be sent to or received from. Master devices can also act as slaves, so that other masters can send information to them. A PC with a P-NET interface is also a master (and slave) device, and one or a number of PCs can be included in the P-NET network. Slaves are normally devices that are connected to sensors and actuators. They usually contain pre-programmed intelligence, in order to provide in-built functionality and to process measurement signals into scaled engineering units.
Uniquely, P-NET is also known as a Multi-net fieldbus. This means that a master that has more that one P-NET port (PD 5000 series, or M36 cluster containing additional P-NET ports), can act as a bridge between 2 independent P-NET segments. This second network can also have 125 nodes connected, and if one of these is a dual-port master, then a further segment can be added, and so on. The great advantage of this property is that designers can structure systems into convenient autonomous segments, perhaps dealing with a particular process or location. Furthermore, it also provides the ability to set up redundancy, where alternative routes can be found between masters and slaves, if the primary route becomes disconnected.
A PC is an important master device in any P-NET system. It can be used to configure and monitor the devices using the VIGO Fieldbus Management System. It is also used as the means for editing, compiling, downloading, and debugging programs written for controllers and DPIs in Process Pascal. It can be used as a permanent SCADA system, graphically displaying and logging the value of measurements, and providing operator control. Due to the facilities offered by P-NET, a number of PCs can be connected to the network at the same time, and PCs can be connected and disconnected during normal operation.
P-NET via cable normally operates at a single speed of 76.8 kbit/s. This enables cables to have lengths of up to 1.2 Km (RS485), without the need for repeaters. Due to the efficiency of the protocol, this allows up to 300 confirmed floating point measurements to be transferred between nodes every second within each P-NET segment. When applied to banks of digital signals (valves etc), it means that multiple activation or deactivation can be achieved in less than 3mS.
Nodes (modules) typically deal with more than one sensor or actuator, where the inputs and outputs provided are connected to digital and analogue devices. P-NET defines that all the data associated with a particular measurement or activating device is partitioned within a module, into what is known as a Channel. A Channel is a highly structured collection of registers, provided either to hold the result of a measurement, or available to set scaling and other configuration data. As such, registers are defined as holding various simple and complex data types (e.g. Real, Integer, Byte, Array, Record, etc.) and can appear in various memory types (e.g. Read/Write, Read Only, Protected Write, etc.). A channel also provides information about the error state of this particular process. For a particular type of input or output, e.g. a digital output, all such channels of this type will be structured in the same way. So, if a module can deal with multiple digital output channels, they will all have the same structure. There are a number of standard channels that have been documented and published. Manufacturers making new devices must register new channel structures with the International P-NET Users Organization (IPUO). Each register has an access address from P-NET called the Softwire Number (SWNo), which together with the node address is the means that devices attached to P-NET can gain access to these registers.
The cable used for connecting remotely located nodes together, is of the screened twisted pair type, similar to the specification defined by IBM Twinax, having a characteristic of 105 ohms and 51 pF per metre.
No special connectors are required to be used with P-NET.
Clusters of M36 modules communicate between themselves within their own local P-NET segment. However, rather than communicating via cable, the communication is via light, using segmented fibre optics (Light-Link P-NET). If the connection between RS 485 P-NET and Light-Link P-NET is direct, e.g. via a Simple P-NET Interface module, then Light-Link operates at the same speed as RS 485. However, if the Light-Link segment is separated from RS 485 via a DPI gateway, e.g. PD 60x, then Light-Link can be configured to operate at up to 230.4 kbits/s
More detailed information about P-NET can be obtained from the International P-NET Users Organization (IPUO), by visiting the IPUO Web site at http://www.p-net.org.